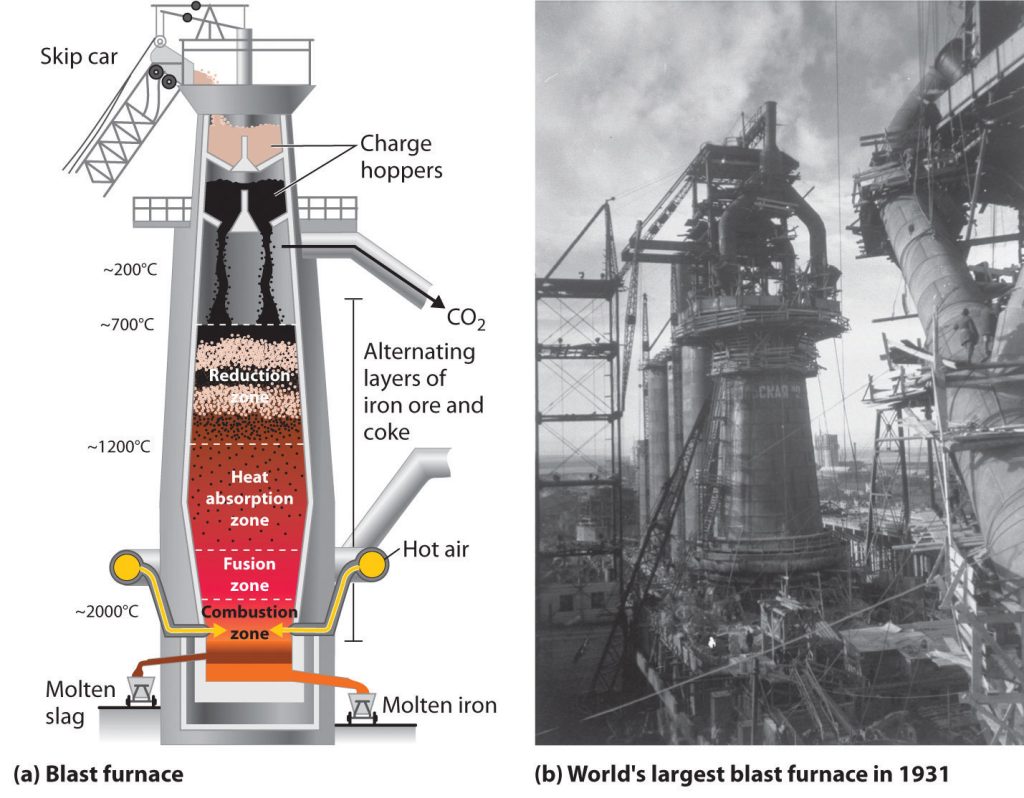
Industrial production of iron involves several processes. These processes include extracting iron ore, crushing and grinding the ore to a fine powder, concentrating the ore, pelletizing the ore, and sintering or melting the ore. The steps may also involve using a blast furnace to reduce the ore to pig iron, and then transforming it into steel. Finally, the steel is formed into products through casting, forging, or rolling.
Fe2O3 + 3CO → 2Fe + 3CO2
C + O2 → CO2
CaCO3 → CaO + CO2
2CaO + SiO2 → 2CaSiO3
This is the reaction used in the Blast Furnace process for the production of iron. In this process, iron ore (Fe2O3), coke (carbon monoxide, CO) and limestone (CaCO3) are heated together in the furnace. The heat causes the coke to react with the oxygen in the air to produce carbon dioxide (CO2). The heat also causes the limestone to decompose into calcium oxide (CaO) and carbon dioxide. Finally, the calcium oxide and the silica in the iron ore react to form molten calcium silicate (CaSiO3). The iron is then extracted from this mixture by reduction with the coke. The carbon dioxide produced in these reactions is then vented out of the furnace.
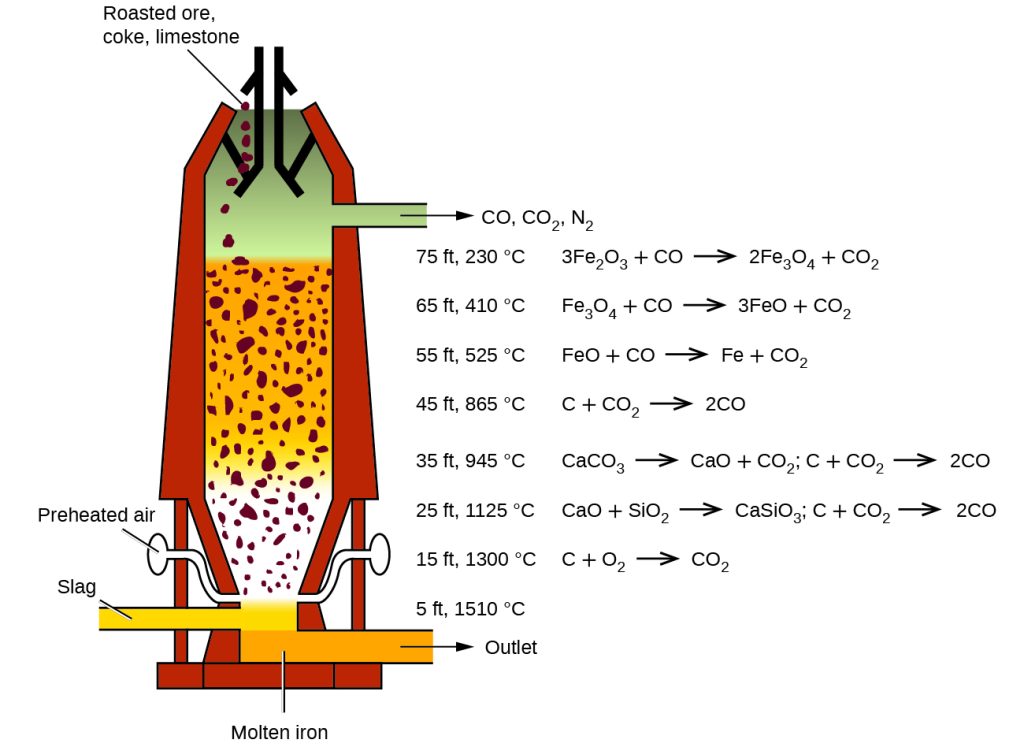